روش های تولید ورق های فولادی
مراحل تولید ورق فولادی را در کارخانه فولاد مبارکه اصفهان
تولید تیرآهن و ورق فولادی در کنار دیگر مقاطع یکی از نشانههای افزایش توانمندی یک کشور در صنعت است. ظرفیت تولید بیش از ۳۰ میلیون تنی فولاد در ایران نشان از قدرت علمی و اجرایی کشور در زمینه صنعت دارد. ایران با داشتن منابع بسیار غنی سنگ آهن مسیر خود را به سمت فراوری و ایجاد ارزش افزوده از طریق آن پیش میگیرد.
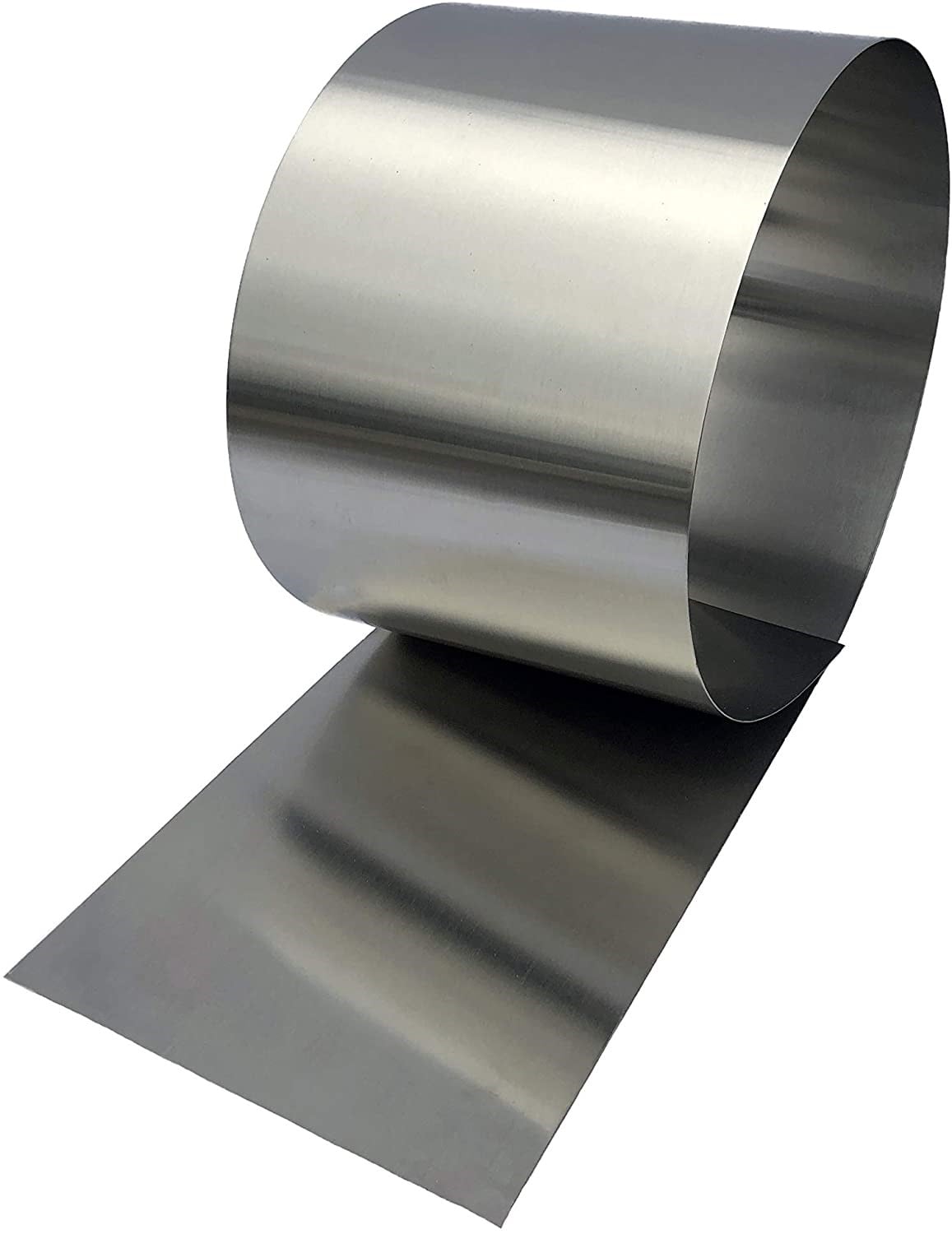
مراحل تولید ورق فولادی آنچنان به ظرافت و پیش نیازهای متعدد نیازمند است که کشورهای محدودی این توانایی را در اختیار دارند. ایران نیز در بین این کشورها قرار گرفته است. در این مقاله مراحل تولید ورق فولادی را در کارخانه فولاد مبارکه اصفهان مورد بررسی قرار میدهیم. در بازار آهن انواع ورق فولادی با آلیاژهای مختلف، به صورت رول و یا برش خورده به فروش میرسد. هر کدام از انواع ورق بسته به ساختار، خواص متفاوتی را از خود نشان میدهند. به همین دلیل این محصول کاربرد بسیار متنوعی در صنایع مختلف دارد.
آشنایی با روند تولید ورق فولادی علاوه بر اینکه جالب است، به مشتری این آگاهی را میدهد تا هنگام خرید دقت کنند. یکی از دلایل متنوع بودن این محصول در بازار، متفاوت بودن روش تولید ورق فولادی است. این مسئله بی شک بر قیمت کالا موثر خواهد بود. برای درک بهتر از تفاوت بر بر روی لینک کلیک کنید.
بر حسب روش تولید ورق فولادی، با دو نوع ورق سرد و ورق گرم مواجه هستید. هر کدام از این دو گروه ورق خواص مکانیکی مختلفی دارند. همچنین گروهی از ورقها به دلیل خاص بودن آلیاژشان گروه متفاوتی را به خود اختصاص میدهند. به دلیل نبودن امکانات تولید ورق فولادی با آلیاژ استیل در ایران، این محصول در گروه کالاهای وارداتی قرار میگیرد. به همین دلیل قیمت آن بر نرخ روز دلار وابستگی دارد. اما به راستی روش تولید ورق فولادی به چه صورت است؟ برای دستیابی به پاسخ این پرسش مطالعه ادامه این مقاله را از دست ندهید.
فرآیند فراوری سنگ آهن
پیش از اینکه تولید ورق قطعات, فولادی را مرور کنیم، باید به سراغ ماده اولیه بریم. سنگ آهن استخراج شده ترکیبی از اکسیدهای آهن و ناخاصیهای بسیاری است. از بین آنها میتوان سولفور، سیلیس و فسفر را نام برد. سنگ آهن پس از استخراج به کارخانه فولاد آورده شده و در ابتداییترین مرحله فراوری و خالص سازی میشود. پس از خرد شدن و جداسازی ناخالصیها به شکل گندله در آمده و با حرارت پخته میشود.
مرحله احیا سنگ آهن
پس از فرآوری سنگ آهن و رسیدن به خلوص مورد نظر و تولید گندله سنگ آهن نیاز است تا به کمک احیا اکسید آهن به آهن تبدیل شود. معمول ترین روش ها استفاده از کوره بلند و کوره احیا مستقیم است. در ایران به غیر از واحد ذوب آهن صفهان که ۳ کوره بلند فعال دارد سایر فولادسازان به کمک روش احیا مستقیم فعالیت میکنند. خروجی احیا مستقیم آهن اسفنجی است که به دلیل تخلخل بالا با این نام شناخته میشود. آهن اسفنجی به صورت بریکت به عنوان شارژ کوره قوس مورد استفاده قرار میگیرد.
شارژ کورههای عظیم قوس الکتریکی
از ترکیب آهن اسفنجی تولید شده و قراضه فولاد میتوان به نام شارژ کوره های قوس الکتریکی یاد کرد. این کورهها ساز و کار مختلفی دارند. اما در معمولترین نوع آن حرارت لازم جهت ذوب آهن به کمک قوس الکتریکی ناشی از جریان الکتریکی وارد شده به الکترودها تامین میشود. دمای قوس تشکیل شده بین الکترودها و الکترود با کف کوره بسیار بالا است. چیزی حدود ۳۰۰۰ درجه سانتیگراد. این دمای بالا امکان ذوب شارژ چند صد تنی را در عرض چند ساعت فراهم میکند. در واقع نرخ انتقال حرارت در کوره قوس بسیار بالا است.
پس از تشکیل مذاب آهن، با چند مرحله دمش اکسیژن و سرباره گیری ناخالصیها از آن جدا و مقادیر کربن کنترل میشود. پس از تایید ترکیب شیمیایی، مذاب به واحد ریختهگری منتقل میگردد.
شمش فولادی متولد میشود
مواد مذاب را در پاتیلهای مخصوص ریخته و دوباره تحت عمل حرارتی قرار داده میشوند. گرمایش در اینجا در کوره ای به اسم ladle furnace صورت میگیرد که به نوعی یک کوره قوس کوچک است. مجددا نمونه گیری ها و آزمایشاتی روی مذاب در این مرحله انجام میشود. نمونه ها برای تایید صحت گرید ایجاد شده به آزمایشگاه فرستاده میشود. مواد مذاب به سرعت حرارت از دست میدهند پس بهتر است بلافاصله عملیات ریخته گری انجام شود. در غیر این صورت هزینه حرارت دهی و نگهداشت دمای ۱۵۸۰ درجه ای مواد مذاب بسیار هزینه بر خواهد بود.
پس از ریختن مواد مذاب فولاد به داخل قالب جریانی از آب به آرامی آهن را سرد میکند و شمش فولادی از دل آن متولد میشود. مرحله تولید شمش فولادی دارای دو قسمت اصلی است. یکی پاتیل بزرگ و حجیم برای قرار گیری مواد مذاب و دیگری محل اصلی برای قالب گیری و ریخته گری آن.
این دو محل جداگانه سرعت عملیات را افزایش داده و به کاهش هزینه برای نگهداشت دمای مواد مذاب کمک مینماید. شمش فولادی به طور کلی در سه نوع بیلت، بلوم و تختال تولید میشود که شما میتوانید برای مطالعه بیشتر مقاله آشنایی با را مطالعه کنید. برای محصول ورق فولادی از شمش تختال یا اسلب استفاده میشود.
نورد گرم و تولید ورق فولادی
در مرحله نورد گرم، شمشهای ایجاد شده در فرایند قبلی ۱۲۰۰ درجه گرم میشوند و سپس به منظور کاهش ضخامت از بین غلتک ها عبور داده میشوند. تا اینجای کار تولید ورق فولادی به انتها نرسیدهاست. این تنها آغاز مراحل پیچیدهتری برای رسیدن به محصول نهایی است. تا اینجای کار ورق فولادی یا ورق فلزی ایجاد شده است. اما این تنها آغاز مراحل پیچیده تری برای رسیدن به محصول نهایی است. تختال (محصول نهایی بدست آمده از نورد گرم فولاد ) دارای ضخامت و عرض زیادی است که باید تحت فرآوری و تبدیل قرارگیرد. این مرحله توسط نورد سرد انجام میشود.
خطوط نورد گرم امروزی معمولا شامل چند فرآیند به شرح زیر میباشند:
کوره های پیش گرم
پوسته شکن
نورد خشن کار
میز انتقال تختال
دستگاه برش و پوسته شکن ثانویه
نورد پایانی
خنک کن های آبی
دستگاه های بسته بندی
گرچه میتوان از محصول نهایی در این مرحله استفاده نمود اما فرایند تولید ورق فولادی هنوز ادامه دارد. در قسمت تکمیل نورد بر پایه سفارش احتمالی مشتری در صورت نیاز فرایند نورد پوستهای روی کلاف انجام میگیرد. پس از آن در قسمت برش سبک و سنگین کلاف را برش داده و به صورت ورق در میآورند. این محصولات گرم عمدتا برای تولید سازههای آهنی سنگین نظیر لوله های انتقال سیالات و … استفاده میشوند.
نورد سرد در تولید ورق فولادی سرد
محصول نهایی مراحل قبل برای تمیزکاری وارد قسمت اسید شویی میشود. کلاف اسید شویی شده نیز میتواند یک محصول نهایی باشد. این کلاف بصورت سر وارد غلتکها شده و با کشش همزمان از بین آنها عبور داده میشود. که باعث کاهش ضخامت آن برای مصارف خاص میگردد.
برای تولید محصولات سرد، کلاف خام تولید شده در فرایندهای ، چرخه بازپخت و اصلاح قرار میگیرد. در صورت نیاز در این مرحله نیز طبق درخواست مشتری، کلاف ایجاد شده پس از طی مراحل قبل سیکلهای برش سبک یا سنگین را طی مینماید. این ورق عمدتا در تولید بدنه خودرو و لوازم خانگی به کار میروند. تولید ورق فولادی میتواند در این مرحله پایان یابد. اما به کمک فرایندهای بعدی میتوان خواص ورق را بهبود بخشید.
پوشش دهی ورق فولادی ، مرحله آخر
ورق فولادی پوششدار در صنایع مختلف کاربرد بسیاری دارد و از تقاضای بالایی برخوردار است. این نوع ورقها شامل ورق گالوانیزه، ورق قلع اندود و ورق رنگی میشوند. کیفیت، رنگ متنوع و مقاومت دربرابر خوردگی در کنار سطح براقتر قسمتی از تمایز ورق پوشش دار در مقایسه با محصولات مرحل قبل است.
در فرایند قلع اندود سطح کلاف با لایه نازکی از قلع پوشش داده میشود. قوطی های حلبی که در سطح بازار مشاهده میکنید و همچنین کاربرد در صنایع غذایی قسمتی از کاربری این محصول است. در فرایند گالوانیزه، سطح ورق با لایه نازک روی پوشش داده می شود. از این محصول برای ساخت مخازن استفاده میکنند. ورق گالوانیزه را می توان به عنوان محصول نیم ساخته در فرایند پوشش رنگی به کار گرفت. در این فرایند سطح ورق فولادی با رنگ های مخصوصی پوشش داده خواهد شد. ورق رنگی بیشتر در صنایع تولید لوازم خانگی و ساخت سوله به کار می رود.
میتوانید قیمت روز ورق گالوانیزه به عنوان پرکاربردترین ورق پوشش دار با کلیک روی لینک زیر مشاهده کنید:
اگر شما نیز نکاتی درباره مراحل تولید ورق فولادی در کارخانه فولاد میشناسید در قسمت نظرات با ما و دیگران به اشتراک بگذارید. همچنین میتوانید برای سفارش و یا استعلام و فولاد با مشاوران بخش بازرگانی (پیشرو صنعت نفت آسیا) تماس حاصل نمایید.
قیمت میلگرد ۱۴ آجدار در بازار آهن آلات به صورت کیلویی اعلام میشود. میلگرد 14 کاربردهای گستردهای در ساختمان سازی و راه سازی دارد. میلگرد۱۴ آجدار a3 و a4 در ساختمان سازی برای انواع مقاطع ستونها کاربرد دارد. قیمت هر شاخه میلگرد ۱۴ بر اساس تفاوتهایی که در قیمتگذاری و وزن هر برند وجود دارد محاسبه میشود. از میلگرد نمره 14 استاندارد a3 و a2 در پی و دیوار حائل و کیسون استفاده میکنند.
میلگرد14 را به عنوان فولاد تقویتی برای کف اتوبانها و جادهها نیز به کار میبرند. دانستن وزن هر شاخه میلگرد ۱۴ کمک میکند تا قیمت روز میلگرد ۱۴ را به صورت شاخهای محاسبه کنید. نرخ میلگرد ۱۴ با توجه به تقاضای بالای آن معمولا با نوساناتی همراه است. در اختیار داشتن قیمت میلگرد ۱۴امروز و مقایسه قیمت آنلاین و قیمت بازار آهن کمک خواهد کرد تا انتخابی هوشمندانه داشته باشید. ۶ برند اصلی تولید کنندهی این میلگرد، نیازهای سراسر ایران را پوشش میدهد و قیمتگذاری این کارخانهها در تعیین نرخ نهایی تاثیرگذار است.
در مرکز ایران قیمت میلگرد۱۴ اصفهان و در جنوب ایران قیمت میلگرد۱۴ اهواز و قیمت میلگرد ۱۴ سیرجان نقشی تعیین کننده در قیمتگذاری بازار دارد. همچنین در مناطق غربی ایران قیمت میلگرد زاگرس ۱۴ در شهرکرد و قیمت میلگرد ۱۴ راد همدان و قیمت میلگرد ۱۴ امیرکبیر ، قیمت میلگرد 14 را تحت تاثیر قرار خواهد داد. در ادامه وزن میلگرد 14 به همراه قیمت هر شاخه میلگرد 14 و مشخصات میلگرد۱۴ آجدار در جدول ها ارائه شده است.
قیمت میلگرد ۱۴امروز
بررسی نمودارهای قیمت میلگرد ۱۴امروز و مقایسه قیمت های بازار نشان میدهد که مسیری دشوار برای انتخاب بهترین گزینه پیش پای خریدار است. در گام اول باید بهترین کیفیت منطبق با نیاز پروژه ساختمانی انتخاب شود. در گام دوم با نگاهی گذرا به قیمت میلگرد 14 امروز و مقایسه آن با روزهای گذشته، عامل زمان در تصمیمگیری لحاظ میشود. برای خرید میلگرد ۱۴قیمت امروز و روزهای پیشین و مقایسه آن با مدت مشابه سال گذشته و در نظر گرفتن شرایط بازار، به خریداران کمک خواهد کرد تا زمان مناسب را برای خرید انتخاب کنند.
قیمت میلگرد 14 آجدار
قیمت میلگرد 14 آجدار عموما برای استاندارد a3 ( آج ۴۰۰ و آج ۴۲۰ – جناقی و یکنواخت ) اعلام میشود و اغلب کارخانهها میلگرد 14 a3 را به بازار عرضه کردند. از این قطر میلگرد در استاندارد a2 ( آج مارپیچ و یکنواخت 320 و 350 ) نیز تولید و به بازار عرضه شده است.
برای خرید میلگرد a2 نمره ۱۴ میتوان از کارخانههای حسن رود، خرمدشت تاکستان ، حدید سیرجان و مهر کیان کاشان اقدام کرد. قیمت میلگرد آجدار ۱۴ استاندارد a2 و a3 تقریبا مشابه است اما استاندارد a4 تا حدودی گرانتر است.
پنج کارخانه در ایران بالاترین استاندارد میلگرد ۱۴ یعنی A4 یا همان آج مرکب را همیشه در سبد تولیدات خود دارند. مهندسان خبره از مزیت میلگردهای این استاندارد مطلع هستند. کارخانه های ذوب آهن هایپر ، کویر کاشان ، ظفر بناب ، امیرکبیر خزر و روهینا دزفول میلگرد۱۴ A4 را روانه بازار کرده اند.
تعیین قیمت میلگرد ۱۴ امروز از عوامل متعددی تاثیر میگیرد. از سیاستگذاریهای کلان اقتصادی گرفته تا جزئیات پروژههای عظیم عمرانی و حتی فصل در قیمت گذاری موثر است. برای پیگیری نوسانات قیمت میتوان به بازار بورس سر زد و نرخ مصوب را بر تابلوی اعلام قیمت مشاهده کرد یا قیمتهای اعلامی تمامی بنگاههای خرید و فروش میلگرد ۱۴ را در سایت عمران مدرن بررسی و با هم مقایسه کرد. قیمت هر کیلو میلگرد ۱۴ اعلام شده توسط تمامی سایتهای فروش میلگرد در ایران به صورت یکجا در اختیار خریداران قرار گرفته است.
قیمت میلگرد۱۴ امروز به صورت مستمر به روزرسانی میشود و آخرین قیمت اعلامی در اختیار خریداران قرار میگیرد. بری دریافت قیمت میلگرد۱۴ امروز از تمامی سایتهای فروش میلگرد آنلاین کافیست ارقام اعلامی از کارخانه ها متفاوت و در تمامی بنگاهها در لیست قیمت ها با هم مقایسه شود.
جدول قیمت میلگرد ۱۴
میلگرد ۱۴ با استاندارد A3 در اغلب کارخانههای فولاد و نورد تولید میشود. جدول زیر شامل لیست قیمت میلگرد14 مربوط به بهار 1401 است. قیمتها همواره در نوسان است و برای قیمتها به صورت مستمر به روزرسانی میشود.
قیمت میلگرد۱۴ اصفهان
قیمت میلگرد 14 اصفهان معمولا به عنوان معیاری برای قیمت گذاری در نظر گرفته میشود. کارخانه ذوب آهن اصفهان بزرگترین تولید کنندهی میلگرد در ایران است. در بخشهای قبلی امروز برای هر کیلو و هر شاخه محاسبه شده. با توجه به اینکه این ذوب آهن اصفهان شرایط فروش از درب کارخانه را ندارد و فروش محصولات این برند توسط واسطهها انجام میشود، پیش از خرید لازم است قیمت میلگرد۱۴ اصفهان امروز از بنگاههای متفاوت آنلاین و حضوری با هم مقایسه شود.
قیمت میلگرد 14 آجدار اصفهان مربوط به هر سه استاندارد A2 و A3 و A4 اعلام میشود. کارخانههای معدودی در ایران توانایی تولید این میلگرد را به صورت آج مرکب دارند و ذوب آهن اصفهان میلگرد نمره۱۴ A4 را با بالاترین کیفیت روانه بازار کرده است و قیمت میلگرد۱۴اصفهان آج مرکب نسبت به سایر استانداردها تا حدودی بالاست. برای محاسبهی قیمت هر شاخه این کارخانه به وزن میلگرد۱۴ اصفهان نیاز خواهید داشت که حدودا با استاندارد اشتال برابری میکند.
قیمت میلگرد ۱۴ سیرجان
کارخانه سیرجان حدید از سال ۹۰ تا به امروز بخش مهمی از نیازهای بازار آهن آلات جنوب ایران را تامین کرده است. این کارخانه در دو استاندارد A3 و A2 میلگرد ۱۴ را روانه بازار میکند. قیمت میلگرد 14 کرمان از برند سیرجان حدید رنج متوسطی دارد و با توجه به کیفیت بالای آن کاملا مقرون به صرفه است. قیمت هر شاخه و هر کیلو میلگرد ۱۴ از برند حدید سیرجان در جداول بالا اعلام شده است.
قیمت میلگرد۱۴ اهواز
در جادهی خرمشهر به اهواز با گروه ملی صنعتی فولاد ایران مواجه خواهید شد که بخش تولید میلگرد آن با نام نورد کوثر شناخته میشود. قیمت میلگرد 14 اهواز مربوط به استاندارد A3 است. این کارخانه علاوه بر میلگرد شاخه ای ، میلگرد را به صورت کلاف نیز تولید و روانه بازار میکند. قیمت الموتور ۱۴ خوزستان مربوط به کارخانههای این منطقه از برند نورد کوثر و قیمت میلگرد اهواز ۱۴ تاثیر زیادی میگیرد. قیمت میلگرد ۱۴ به صورت هر کیلو و هر شاخه از میلگرد کوثر اهواز در جداول بالا بررسی شده است.
قیمت میلگرد زاگرس ۱۴
کارخانه زاگرس شهرکرد از معدود کارخانههایی است که توانایی تولید میلگرد آج ۵۰۰ را دارد. قیمت میلگرد 14 زاگرس بر اساس استاندارد a3 و a4 با هم متفاوت است. قیمت میلگرد 14 زاگرس امروز در جداول بالا اعلام شده است. با توجه به صادرات محصولات کارخانه زاگرس و حضور در بازار بورس، قیمت میلگرد ۱۴ زاگرس بر اساس شرایط عرضه و تقاضای بازار و سیاستگذاری کارخانه تعیین میشود.
تولید ورق های فولادی که سال هاست در تمام صنایع کاربرد دارند نمادی از قدرت یک کشور در عرصه فن آوری و تولیدات است. ایران نیز مانند اغلب کشورهای قدرتمند دنیا در زمینه تولید ورق های فولادی دستی بر آتش دارد. از آنجا که ایران خود یکی از منابع غنی سنگ آهن شناخته می شود، کارخانه های زیادی در کشور ما تاسیس شده و هر کدام به نحوی در فرآیند تولید ورق فولادی تلاش می کنند. البته انجام فرآیند تولید ورق آهن آنهم به درستی و بدون هیچ عیب و نقصی راحت نبوده و رعایت ظرافت و پیش نیازهایی برای انجام آن واجب است. در مقاله حاضر با روش ها و مراحل تولید ورق فولادی آشنا می شویم؛ بنابراین پیشنهاد می کنیم که تا پایان همراه ما بمانید.
روش کلی تولید ورق فولاد در کارخانه ها
می دانیم که ورق های فولادی به دو روش نورد گرم و نورد سرد تولید می شوند، اما اجازه دهید تا ابتدا با صفر تا صد مراحل تولید ورق فولادی در کارخانه آشنا شده و در عین حال فرآیندهای نورد را بشناسیم. در واقع شروع مراحل تولید ورق فولادی در کارخانجات از تولید آهن خام کلید خورده و تا تولید ورق های فولادی ادامه پیدا می کند که به صورت زیر هستند:
فرآوری سنگ آهن اولیه استخراج شده
تولید آهن اسفنجی
تولید شمش فولاد (تختال)
تبدیل شمش فولادی به کلاف های نرم از طریق فرآیند نورد گرم
تولید کلاف های نرم از طریق فرآیند نورد سرد
انجام عملیات تکمیلی تولید فولاد و محصول نهایی کلاف
انجام آخرین مرحله و پوشش دهی به ورقه های فولادی مانند گالوانیزه، رنگی و…
اما ببینیم هر کدام از مراحل تولید ورق فولادی به چه صورتی و با چه فرآیندی انجام می شوند؟
فرآوری سنگ آهن اولیه استخراج شده
در مرحله اول، که ابتدایی ترین و شروع فرآیند تولید ورق فولادی شناخته می شود، طی عملیاتی خاص، ناخالصی فلزی را از سنگ آهن خرد شده جدا کرده و طی فرآیندی به نام گندله سازی و پختن سنگ آهن مذکور، آن را به شکل گلوله در می آورند تا آماده استفاده شود.
تولید آهن اسفنجی
در مرحله دوم از گندله تولید شده در فرآیند احیا مستقیم با عنصر کربن واکنش پیدا کرده و آهن خالص را تولید می کند. از آنجا که در طی این مرحله گندله اکسیژن خود را از دست خواهد داد بنابراین حالتی تخلخلی و به شکل اسفنج به خود می گیرد که به همین دلیل آن را آهن اسفنجی نیز می گویند. این آهن اسفنجی را به تدریج به عنوان ماده اولیه تولید فولاد در سایر مراحل تولید ورق فولادی مورد استفاده قرار می دهند.
تولید شمش فولاد ( تختال )
در سومین مرحله از مراحل تولید ورق فولادی، فولاد مذاب را در پاتیل های حجیمی خالی و جهت انجام عملیات تکمیلی ارسال می کنند. فولاد مذاب با دمایی نزدیک به 1650 درجه سانتی گراد باید بعد از عملیات تکمیلی وارد مرحله ریخته گری شود. پس از این مرحله، فولاد مذاب تولید شده که وارد ماشین های ریخته گری شده اند به صورت شمش یا تختال درآمده و پاتیل های مذاب را بر روی برج ریخته گری که قادر است تا دو پاتیل را در خود نگه دارد، قرار می دهند.
در نهایت پس از فرآیندهای حاشیه ای دیگر مانند تاندیش و توالی مواد مذاب در قالب تخلیه شده و توسط جریان آب اطراف قالب ها خنک و با طی یک مسیر نیم قوسی به شکل نواری طولانی با یک مقطع مستطیل شکل از ماشین ریخته گری خارج شده و شمش های فولادی را شکل می دهند.
تبدیل شمش فولادی به کلاف های نرم از طریق فرآیند نورد گرم
در مرحله چهارم، فرایند نورد گرم بر روی فولاد صورت می گیرد. در این مرحله از مراحل تولید ورق فولادی نیز فرآیند تختال یا همان شمش فولاد را در کوره های مخصوص تا دمای 1200 درجه سانتی گراد گرم کرده تا زمانیکه سرخ و شکل پذیر شود. تختال سرخ شده را از بین غلتک های نورد عبور داده تا ضخامت آن کاهش یابد. در آخر پس از خنک کاری آن را به صورت کلاف گرم از دستگاه خارج می کنند. تختال حاصل شده در این مرحله را هم می توان به صورت مستقیم به کار برد و هم آن را وارد فرآیندهای بعدی مثل نورد سرد یا تکمیل نورد کرد.
اما شاید بپرسید مرحله تکمیل نورد چیست؟ در این مرحله در صورتیکه مشتری سفارش داده باشد فرآیند اسکین پاس(نورد پوسته ای) روی کلاف انجام شده و در خطوط برش سبک و سنگین، کلاف را برش داده و به صورت محصول نهایی و تکمیل شده مورد استفاده قرار می دهند. از ورق های فولاد تهیه شده به روش نورد گرم اغلب در تولید لوله های انتقال سیالات، سازه های سنگین و گسترده و… استفاده می شود.
تولید کلاف های نرم از طریق فرآیند نورد سرد
در پنجمین مرحله، فرآیند نورد سرد بر روی ورق های فولادی شکل می گیرد. در این فرآیند ابتدا کلاف های گرم را از فرآیند اسیدشویی رد کرده تا سطح ورق کاملا صاف و تمیز شود، بدین جهت است که به این محصول کلاف اسیدشویی نیز گفته می شود. پس از اسید شویی است که کلاف مورد نظر وارد فرآیند نورد سرد خواهد شد. در این فرایند کلاف های اسیدشویی شده که تقریبا سرد شده اند را از میان غلتک هایی عبور داده تا با فشار غلتک ها ضخامت کلاف نازک تر از قبل شود.
محصولی که از این فرآیند به جا می ماند یک کلاف خام است. از این کلاف خام هم می توان به صورت مستقیم استفاده کرد و هم آن را وارد فرآیندهای بعدی کرد. در فرآیند نورد است که کلاف خام مرحله سیکل های بازپخت، نورد پوسته ای و اصلاح ورق فولادی را طی کرده و آماده استفاده می شود. معمولا ورق های تهیه شده به روش نورد سرد در ساخت لوازم خانگی، فیلتر، بدنه و داخل خودروها و… مورد استفاده قرار می گیرند.
پوشش دهی به ورقه های فولادی مانند گالوانیزه، رنگی و …
در مرحله ششم از مراحل تولید ورق فولادی که مرحله نهایی نیز شناخته می شود عملیات پوشش دهی ورق انجام می شود. ورق های فولادی پوشش دار که غلب به صورت رنگی، گالوانیزه یا قلع اندود هستند از باکیفیت ترین و مقاوم ترین ورق ها در برابر هر گونه زنگ زدگی و ضربه بوده که مصارف ویژه ای دارند. برای مثال ورق های قلع اندود دارای سطحی پوشیده شده از عنصر قلع می باشد که این پوشش به صورت یک لایه نازک سطح ورق را در برگرفته است. ورق های قلع اندود عموما در تولید قوطی ها و بسته بندی های مواد غذایی و قوطی های حلبی مورد استفاده قرار می گیرند.
در فرآیند گالوانیزه نیز سطح ورق با یک لایه نازک از عنصر روی پوشیده شده که اغلب این ورق های گالوانیزه را در ساخت مخازن مورد استفاده قرار می دهند. معمولا ورق های گالوانیزه را نیز می توان به عنوان محصول نیم ساخته در فرآیندهایی که به پوشش رنگی نیازمند هستند به کار گرفت. اما فرآیند پوشش رنگی یعنی چه؟ در این فرآیند از ورق های فولادی با سطحی پوشیده شده از رنگ برای لایه هایی که در دید هستند، استفاده می کنند. از این ورق برای ساخت ابزارهایی مانند سوله ها، لوازم خانگی و … استفاده می کنند.
انجام صحیح تمامی مراحل فوق بر کیفیت ورق های فولادی مانند ورق رنگی ، گالوانیزه و .. تاثیر گذار میباشد که البته یکی از عوامل تعیین کننده قیمت انواع ورق ها نیز همین کیفیت ساخت کارخانه تولید کننده آن می باشد. برای مشاهده بر روی این لینک کلیک نمایید.
کلام آخر
این روزها ورق های فولادی در نود درصد صنایع کاربرد داشته و به نوعی پای ثابت ساخت بسیاری از لوازم و ابزارهای صنعتی اطراف ما هستند. اما این ورق ها از ابتدا به صورت شیک و منظم نبوده بلکه در مراحل مختلفی به این شکل در می آیند. در واقع این سنگ آهن است که مواد اولیه ساخت این ورق ها را تشکیل داده و پس از طی فرآیندهایی به شکل نهایی خود در آمده و در صنایع به کار می روند. از اصلی ترین مراحل تولید ورق فولادی می توان به دو فرآیند نورد گرم و نورد سرد اشاره نمود که تا حدودی با آن ها آشنا شدیم. این ورق ها کاربردی اساسی و مهم در ساخت و سازها نیز دارند پس هیچگاه ارزش آنها را نادیده نگیرید.